Инструкция По Визуально Измерительному Контролю
Визуальный и измерительный контроль — самый простой и в то же время информативный метод контроля. Это единственный метод неразрушающего контроля, который может выполняться и часто выполняется без какого-либо оборудования или проводится с использованием простейших измерительных средств. Он позволяет выявлять поверхностные поры и трещины, подрезы, кратеры, прожоги, свищи, наплывы, смещения кромок и другие дефекты. К недостаткам метода можно отнести низкую вероятность обнаружения мелких поверхностных дефектов, а также зависимость выявляемости дефектов от субъективных факторов (острота зрения, усталость, опыт работы выполняющего контроль специалиста) и условий контроля (освещенность, оптический контраст и др.).
- Инструкция По Визуальному И Измерительному Контролю Казахстан
- Инструкция По Визуальному И Измерительному Контролю Скачать Бесплатно
- Инструкция По Визуальному И Измерительному Контролю Рк
Тем не менее простота, малая трудоемкость и определенная информативность визуального и измерительного контроля делают его обязательным и предшествующим проведению неразрушающего контроля другими методами. Какими бы уникальными ни были методы и средства последующих контрольных операций, контроль изделий начинается с визуального осмотра невооруженным глазом. На оптимальном для глаз расстоянии-250 мм различают детали размером 0,15 мм, однако возможности глаза ограничены при осмотре удаленных, движущихся, недостаточно освещенных объектов.
Наличие грубых поверхностных дефектов может указать на характер и место возможного разрушения конструкции. Учитывая, что различные дефекты имеют определенные доминирующие причины их образования, по результатам визуального и измерительного контроля можно ориентировочно оценить качество и стабильность технологического процесса изготовления или ремонта конструкций.
По визуальному и измерительному контролю*1. РД 03-606-03. _____ *1 Печатается по 'Российской газете' от 21 июня 2003 г., N 120/1.. Подготовка контролируемых поверхностей в обязанности специалиста по контролю не входит. Визуальный и измерительный контроль при техническом диагностировании (освидетельствовании) оборудования, работающего под давлением, следует проводить после прекращения работы указанного оборудования, сброса давления, охлаждения, дренажа, отключения от другого оборудования, если иное не предусмотрено действующей ПТД. Терминология РД 03 606 03: Инструкция по визуальному и измерительному контролю: Асимметрия углового шва Несоответствие фактического. РД 03-606-03 Инструкция по визуальному и измерительному контролю. Утверждены постановлением Госгортехнадзора РФ от №92. Об утверждении Инструкции по визуальному и измерительному контролю. Федеральный горный и промышленный надзор россии. От 11 июня 2003 года N 92. Об утверждении 'Инструкции по визуальному и измерительному контролю'. Госгортехнадзор России постановляет: 1. Утвердить 'Инструкцию по визуальному и измерительному контролю'*. _ * Госгортехнадзором России 'Инструкциям по визуальному и измерительному контролю' присвоено обозначение РД 03-606-03. - Примечание изготовителя базы данных.
По внешнему виду сварного шва можно ориентировочно судить о внутреннем качестве шва. Превышение усиления сварного шва характерно для неполного проплавления кромок.
Подрез на одной стороне сварного шва и наплыв на другой указывают на возможность непровара по кромке со стороны наплыва. При наличии поверхностных пор и грубой чешуйчатости шва, как правило, имеются и внутренние поры. Визуально-измерительный контроль сосуда проводится аттестованными специалистами с целью выявления дефектов, которые могли возникнуть как в процессе его эксплуатации, так и при его изготовлении, транспортировке и монтаже. При осмотре защитные покрытия и изоляция подлежат удалению на участках поверхности сосуда, где имеются явные признаки нарушения их целостности. Необходимость удаления защитного покрытия и изоляции на других участках поверхности сосуда определяется специалистами организации, проводящей диагностирование. Осмотру подлежат все доступные сварные соединения сосуда и его элементы с целью выявления в дефектов: Особое внимание следует обратить на состояние сварных соединений в зонах концентрации напряжений (места приварки горловины люка и штуцеров к обечайке и днищам, особенно зоны входных и выходных штуцеров, участки пересечения швов, зоны сопряжения обечайки с днищами и др.), а также в местах возможного скопления конденсата и зонах проведенного ранее ремонта. Для сосудов из аустенитных сталей особое внимание при осмотре следует уделять местам возможного попадания на поверхность сосуда воды, паров, влажных газов, ввиду возможного образования в этих местах коррозионных трещин.
При проведении осмотра в случае возникающих сомнений по классификации размерам выявленных дефектов следует применять лупу 4 - 20-ти кратного увеличения, а также по усмотрению специалиста выполняющего осмотр, любой из неразрушающих методов в соответствии с РД 03-421-01. Оценка выявленных при осмотре деформированных участков поверхности сосуда производится путем замера максимального прогиба и площади деформированного участка. Замер производится мерительным инструментом, обеспечивающим погрешность ±1,0 мм.
Нормы допустимых дефектов выявленных при наружном и внутренним осмотре, должны соответствовать требованиям ПБ 03-576-03, ОСТ 26-291. Результаты осмотра оформляются в виде заключения (протокола), подписываемого специалистами организации, проводящей диагностирование. Первый руководящий документ по визуальному и измерительному контролю, который распространялся на оборудование, подконтрольное Госгортехнадзору России, был разработан АНТЦ «Энергомонтаж». Несмотря на всю необходимость и своевременность выхода документа, он имел рад существенных недостатков. Документ был ориентирован в основном на объекты котлонадзора и не учитывал конструктивных особенностей грузоподъемных и горно-транспортных машин, в которых наряду со стыковыми широко применяются тавровые, угловые и нахлесточные сварные соединения. Отмеченные недостатки были учтены при разработке РД 03-606-03, который применяется при контроле конструкций грузоподъемных и горно-транспортных машин.
При разработке РД 03-606-03 были использованы положения ЕН 970:1997 «Неразрушающий контроль сварных швов, выполненных плавлением. Визуальный контроль». Толщинометрия Для измерения толщины стенок аппарата и других деталей в результате износа и коррозии используют приборы, работающие на различных физических принципах: радиометрии, акустики (импульсные, по фазе прошедших через изделие ультразвуковых волн, резонансные), магнитных полей, радиоволновые и др. Наибольшее распространение нашли ультразвуковые контактные толщиномеры, позволяющие обследовать объекты с односторонним доступом. Ультразвуковая толщинометрия (УЗТ) применяется с целью определения количественных характеристик утонения стенок элементов сосуда в процессе его эксплуатации.
По результатам УЗТ определяют скорость коррозионного или коррозионно-эрозионного изнашивания стенок и устанавливают расчетом на прочность допустимый срок эксплуатации изношенных элементов, уровень снижения рабочих параметров или сроки проведения восстановительного ремонта. Для измерений толщины металла могут быть использованы отечественные или зарубежные ультразвуковые толщиномеры, соответствующие требованиям действующей нормативной документации, обеспечивающие погрешность измерения не более ±0,1 мм. Все приборы должны иметь паспорт ежегодной метрологической Госповерки.
Контроль толщины стенки проводят в местах элементов сосуда, указанных в специальных инструкциях, в типовых или индивидуальных программах диагностирования, а также в зонах интенсивного коррозионно-эрозионного износа металла, в местах выборок дефектов и на поверхности вмятин или выпучин. Толщинометрия согласно РД 03-421-01 может проводиться как по наружной, так и по внутренней поверхности сосуда. Измерения осуществляются по 4-м образующим обечайки и 4-м радиусам днищ через 90° по окружности элемента. На каждой царге обечайки сосуда проводится не менее 3-х измерений по каждой образующей (середине и по краям). На днищах проводится не менее 5-ти измерений: на каждом из 4-х радиусов и в центре.
При обнаружении зон с расслоением металла число точек измерения в этом месте должно быть увеличено до количества, достаточного для установления границ (контура) зоны расслоения. Измерения толщины стенки вварных патрубков диаметром d 0 - диаметр отверстия не требующий укрепления, согласно ГОСТ 24 755, (Приложение 3) и более следует проводить в одном сечении в четырех точках, расположенных равномерно по окружности элемента. В случае невозможности выполнения УЗТ сосуда по полной программе число точек замера толщины стенок должно быть таким, чтобы обеспечить максимально надежное представление о состоянии сосуда и проведение прочностных расчетов.
В местах измерения толщины поверхность должна быть защищена от металлического блеска. Толщина металла определяется как среднее значение результатов 3-х измерений. Результаты УЗТ элементов сосуда рекомендуется оформлять в виде заключений или протоколов, в которых следует приводить схему расположения мест замера толщины и таблицу значений измеренной толщины. Существуют два метода ультразвуковой толщинометрии: эхоимпульсный и резонансный. При эхоимпульсной толщинометрии измеряют временной интервал между зондирующим и одним из отраженных импульсов.При этом измеряемая толщина определяется из выражения,где t-измеренный интервал, -скорость ультразвука в данном материале. Для импульсной толщинометрии используют прямые преобразователи или, чаще РС-преобразователи.
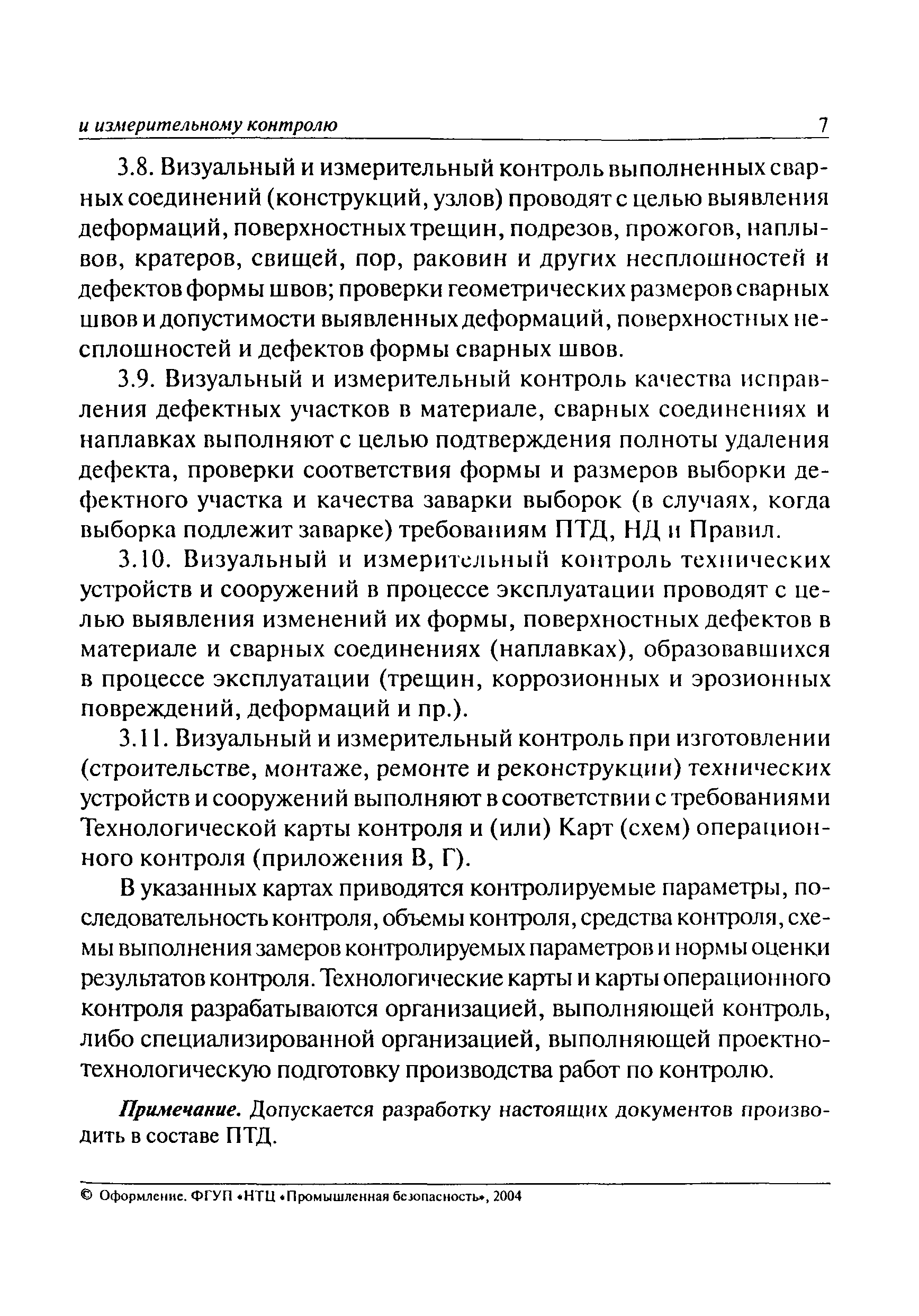
Последние имеют значительно меньшую мертвую зону, что позволяет на практике на частоте 5-10МГц измерять изделия толщиной 1,0-1,5мм и выше. На погрешность измерений существенно влияет качество поверхности и длительность импульса. Повышение качества поверхности (например, до ) и снижение длительности импульса с обычно применяемых значений до мкс позволяет производить импульсным методом измерение металлических изделий толщиной от мм. Относительная погрешность измерения%. Импульсные цифровые толщиномеры относительно просты по конструкции и удобны в эксплуатации. Габаритные размеры лучших из них не превышают пачку сигарет.
Резонансная толщинометрия основана на измерении частот акустических резонансов,возбуждаемых в контролируемом изделии при модулировании (изменений) частоты возбуждаемых ультразвуковых колебаний. Если в изделии возбуждаются резонансы на частотах и,то толщину находят из выражения, и -номера гармоник, а -скорость ультразвука в изделии.
В резонансных толщиномерах пьезопластина преобразователя включена в колебательный контур автогенератора, в цепи которого находится сердечник с переменной индуктивностью. Изменение индуктивности приводит к модуляции частоты колебательного контура и, следовательно, к модуляции частоты возбуждаемых ультразвуковых колебаний. Переменное намагничивание сердечника осуществляется треугольным импульсом генератора временной развертки с экспоненциально спадающей амплитудой. При установлении акустического резонанса в стенке изделия резко изменяется постоянная тока автогенератора и срыв генерации, что фиксируется на стрелочном, цифровом или панорамном проградуированном индикаторе.
Погрешность резонансных толщиномеров%. Однако они более капризны в эксплуатации, имеют относительно большие габаритные размеры и в настоящее время применяются весьма редко. Ультразвуковая толщинометрия легко автоматизируемый процесс.
Иммерсионные толщиномеры широко применяют при сортировке труб, листа, прутков и т. На погрешность ультразвуковой толщинометрии оказывает влияние отклонение геометрии контролируемого слоя от эквидистантности; непостоянство и неоднородность свойств материала, например затухания и скорости УЗК; нарушение акустического контакта или изменение толщины контактного слоя; ошибки в настройке прибора и т. Погрешность большинства контактных резонансных толщиномеров составляет% измеряемой толщины.
Погрешность современных импульсных толщиномеров, например УТ-93П, составляет мм в диапазоне толщин мм и мм в диапазоне толщин мм, где - толщина изделия. Толщиномер УТ-93П производственного объединения 'Волна' (г. Кишенев) комплектуется шестью типами преобразователей на номинальные частоты МГц. Толщиномер УТ-93П имеет расширенный в сторону малых толщин диапазон измерений, уменьшенную погрешность измерения, повышенную устойчивость к воздействию окружающей среды. Прибор снабжен системой автоматического выключения, срабатывающей через 1.5-4.5 мин после последнего измерения, а также при снижении напряжения источника питания ниже предельно допустимого значения.
Измерения производят только после обеспечения акустического контакта преобразователя с поверхностью контролируемого изделия, о чем сигнализирует подсветка служебного знака (точки) после младшего разряда цифрового индикатора. Результат последнего измерения сохраняется в цифровой памяти толщиномера и воспроизводится на индикаторе даже при снятии преобразователя с изделия.
Имеются также другие толщиномеры например: толщиномер Булат-1S(г.Санкт-Петербург, Россия). Ультразвуковой толщиномер Булат-1-S Отличается отсутствием органов регулировки и настройки, прост и удобен в работе, обладает высокой чувствительностью. Исполнение датчиков (корпуса из металла, многожильный кабель с внутренней металлической оплеткой, контактные поверхности и разделительный слой из синтетических полимерных материалов нового поколения с высокими механическими износостойкими свойствами ) обеспечивает их долговечность при эксплуатации в самых тяжелых условиях, в том числе при контроле корродированных поверхностей с большой шероховатостью. Комплектование толщиномера несколькими датчиками обеспечивает широкий диапазон измерения (от 1,5 до 100 мм), возможность контроля изделий с сильно отличающимися геометрическими и физико-механическими свойствами.
РД 03-606-03 ИНСТРУКЦИЯ ПО ВИЗУАЛЬНОМУ И ИЗМЕРИТЕЛЬНОМУ КОНТРОЛЮ I. ОБЛАСТЬ ПРИМЕНЕНИЯ Настоящая Инструкция устанавливает порядок проведения визуального и измерительного контроля основного материала (далее - материала) и сварных соединений (наплавок) при изготовлении, строительстве, монтаже, ремонте, реконструкции, эксплуатации, техническом диагностировании (освидетельствовании) технических устройств и сооружений, применяемых и эксплуатируемых на опасных производственных объектах, подконтрольных Госгортехнадзору России. Визуальный и измерительный контроль специальных материалов (например, композитных и полимерных) и специальных сварных соединений (например, муфтовой сварки) технических устройств и сооружений проводят в соответствии с требованиями специально разработанной документации. ТЕРМИНЫ И ОПРЕДЕЛЕНИЯ Настоящая Инструкция базируется на терминах и определениях, приведенных в правилах безопасности, утвержденных Госгортехнадзором России (далее - Правила), а также использует термины и определения, приведенные в приложении А.
Диапазон измеряемой величины, мм Погрешность измерений, мм До 0,5 вкл. 0,1 Свыше 0,5 до 1,0 вкл. 0,2 ' 1,0 ' 1,5 ' 0,3 ' 1,5 ' 2,5 ' 0,4 ' 2,5 ' 4,0 ' 0,5 ' 4,0 ' 6,0 ' 0,6 ' 6,0 ' 10,0 ' 0,8 ' 10,0 1,0 5.4. Для определения шероховатости и волнистости поверхности следует применять профилографы-профилометры, аттестованные образцы шероховатости (сравнения), а также другие средства измерения. Измерительные приборы и инструменты должны периодически, а также после ремонта проходить поверку (калибровку) в метрологических службах, аккредитованных Госстандартом России. Срок проведения поверки (калибровки) устанавливается нормативной технической документацией (НД) на соответствующие приборы и инструменты. ТРЕБОВАНИЯ К ВЫПОЛНЕНИЮ ВИЗУАЛЬНОГО И ИЗМЕРИТЕЛЬНОГО КОНТРОЛЯ 6.1.
Подготовка мест производства работ 6.1.1. Визуальный и измерительный контроль рекомендуется выполнять на стационарных участках, которые должны быть оборудованы рабочими столами, стендами, роликоопорами и другими средствами, обеспечивающими удобство выполнения работ.
Визуальный и измерительный контроль при монтаже, строительстве, ремонте, реконструкции, а также в процессе эксплуатации технических устройств и сооружений выполняется на месте производства работ. В этом случае должно быть обеспечено удобство подхода специалистов, выполняющих контроль, к месту производства контрольных работ, созданы условия для безопасного производства работ, в том числе в необходимых случаях должны быть установлены леса, ограждения, подмостки, люльки, передвижные вышки или другие вспомогательные устройства, обеспечивающие оптимальный доступ (удобство работы) специалиста к контролируемой поверхности, а также обеспечена возможность подключения ламп местного освещения напряжением 12 В. Участки контроля, особенно стационарные, рекомендуется располагать в наиболее освещенных местах цеха, имеющих естественное освещение. Для создания оптимального контраста дефекта с фоном в зоне контроля необходимо применять дополнительный переносной источник света, то есть использовать комбинированное освещение. Освещенность контролируемых поверхностей должна быть достаточной для надежного выявления дефектов, но не менее 500 Лк. Окраску поверхностей стен, потолков, рабочих столов и стендов на участках визуального и измерительного контроля рекомендуется выполнять в светлых тонах (белый, голубой, желтый, светло-зеленый, светло-серый) для увеличения контрастности контролируемых поверхностей деталей (сборочных единиц, изделий), повышения контрастной чувствительности глаза, снижения общего утомления специалиста, выполняющего контроль. Для выполнения контроля должен быть обеспечен достаточный обзор для глаз специалиста.
Подлежащая контролю поверхность должна рассматриваться под углом более 30° к плоскости объекта контроля и с расстояния до 600 мм (рис.1). Условия визуального контроля 6.2. Подготовка к контролю 6.2.1. Подготовка контролируемых поверхностей проводится подразделениями организации, выполняющей работы по визуальному и измерительному контролю, а в процессе эксплуатации технических устройств и сооружений - службами организации, которой принадлежит контролируемый объект. Подготовка контролируемых поверхностей в обязанности специалиста по контролю не входит. Визуальный и измерительный контроль при техническом диагностировании (освидетельствовании) оборудования, работающего под давлением, следует проводить после прекращения работы указанного оборудования, сброса давления, охлаждения, дренажа, отключения от другого оборудования, если иное не предусмотрено действующей ПТД. При необходимости внутренние устройства должны быть удалены, изоляционное покрытие и обмуровка, препятствующие контролю технического состояния материала и сварных соединений, частично или полностью сняты в местах, указанных в Программе технического диагностирования (освидетельствования).
Перед проведением визуального и измерительного контроля поверхность объекта в зоне контроля подлежит зачистке до чистого металла от ржавчины, окалины, грязи, краски, масла, влаги, шлака, брызг расплавленного металла, продуктов коррозии и других загрязнений, препятствующих проведению контроля (на контролируемых поверхностях допускается наличие цветов побежалости, в случаях, когда это оговорено в производственно-технической документации (ПТД). Зона зачистки должна определяться НД на вид работ или на изготовление изделия. Измерительный контроль проводится с целью измерения размеров сварных швов и поверхностных дефектов, выявленных при визуальном контроле, а также подтверждения соответствия основных размеров изделий (деталей, сборочных единиц) требованиям стандартов, ТУ и паспортов изделий.
Измерительный контроль сварных швов выполняют через один метр по длине каждого контролируемого шва, но не менее чем в трех сечениях сварного шва. Контролируемые параметры и требования к визуальному и измерительному контролю полуфабрикатов (труб, листов, поковок, штамповок) приведены в табл.2. Визуальный и измерительный контроль геометрических размеров кромок деталей, сборочных единиц, а также сварных соединений должен выполняться согласно указаниям, приведенным в подразделах 6.4 и 6.5. Контролируемые параметры и требования к визуальному и измерительному контролю полуфабрикатов. Контролируемый Параметр Вид контроля Требования к контролю 1 2 3 1. Наружный диаметр ( ), внутренний диаметр ( ) Измерительный Измерение и с обоих концов трубы.
Инструкция По Визуальному И Измерительному Контролю Казахстан
Измерение производится при поставке труб по внутреннему диаметру. Толщина листа, стенки трубы ( ) То же Измерение с обоих концов трубы не менее чем в двух сечениях. Измерение листа не менее чем в двух сечениях (по длине, ширине) с каждой стороны листа. Овальность трубы ' Измерение размера с обоих концов трубы.
Кривизна трубы ( ) ' Измерение кривизны на участке 1 м в двух сечениях по длине. Длина трубы, листа ' Измерение не менее 3 труб (листов) из партии 6.
Инструкция По Визуальному И Измерительному Контролю Скачать Бесплатно
Ширина листа ' Измерение не менее 3 листов от партии 7. Трещины, плены, рванины, закаты, раковины, расслоения Визуальный Осмотр наружной поверхности невооруженным глазом; осмотр внутренней поверхности труб невооруженным глазом (при наличии доступа) и с помощью перископа, эндоскопа и пр. Разрешаются вырезка контрольных образцов длиной 200 мм в количестве не менее 2 шт. И их осмотр после разрезки.
Примечания: 1. Контролю по п.1-4 подлежат не менее 50% труб (листов) от партии. Контролю по п.7 подлежит не менее 10% длины каждой трубы (площади поверхности листа). Визуальный и измерительный контроль качества материала полуфабрикатов, заготовок, деталей и изделий проводится согласно Программе (плану, инструкции) входного контроля (приложение Б). В Программах должны указываться контролируемые параметры и способы их контроля. Объемы контроля контролируемых параметров выбираются согласно требованиям стандартов, ТУ, НД или ПТД, а в случае отсутствия требований к объемам контроля в этих документах объем контроля устанавливается согласно требованиям настоящей Инструкции. Порядок выполнения визуального и измерительного контроля подготовки и сборки деталей под сварку 6.4.1.
Контролируемый параметр Условное обозначение параметра Номер рисунка Средства измерений. Требования к измерениям 1 2 3 4 1.
Перпендикулярность кромки 2, а Угломер или шаблон универсальный. Измерение в одном месте 2.
Угол скоса кромки 2, б, в, ж, з, и, л, м, р, ю Угломер или шаблон универсальный. Измерение в одном месте 3.
Притупление кромки 2, б, в, ж, з, и, ю Штангенциркуль. Измерения в двух взаимно перпендикулярных сечениях (4 точки) труб; измерения не менее чем в трех точках по длине в соединениях листов 4. Глубина скоса кромки 2, в, г, д Размер справочный, измерению не подлежит 5. Ширина подкладки в замковом соединении 2, е, ж Штангенциркуль, линейка.
Измерения не менее чем в трех точках по длине 6. Толщина подкладки в замковом соединении 2, е, ж То же 7.
Угол скоса поверхности соединяемого элемента 2, г, д Угломер или шаблон универсальный. Измерение в одном месте 8. Отклонение торца разделки (трубы) от перпендикуляра к образующей трубы 2, к Угольник и щуп (отвес и линейка или щуп). Измерения не менее чем в трех сечениях в зоне максимального смещения 9. Высота присадочного выступа 2, м Штангенциркуль. Измерения в двух взаимно перпендикулярных сечениях (4 точки) 10.
Длина расточки (раздачи) труб по внутреннему диаметру 2, н То же 11. Угол выхода резца (калибра) 2, н, п Шаблон универсальный или угломер, измерение в одном месте 12. Диаметр расточки Д 2, н, п Штангенциркуль. Измерения в двух взаимно перпендикулярных сечениях (4 точки) 13. Номинальная толщина стенки в месте расточки 2, н, п Штангенциркуль. Измерения не менее чем в трех точках равномерно по толщине 14. Ширина подкладной пластины 2, с Штангенциркуль.
Измерения не менее чем в трех точках по длине 15. Толщина подкладной пластины 2, с То же 16.
Ширина подкладного кольца 2, т, у, ф Штангенциркуль. Измерения не менее чем в трех точках по длине (периметру) 17.
Толщина подкладного кольца 2, т, у, ф То же 18. Притупление подкладного кольца 2, т, у, ф То же 19. Диаметр расплавляемого кольца (вставки) 2, ф, х Штангенциркуль. Измерения в двух взаимно перпендикулярных сечениях (4 точки) 20. Толщина расплавляемого кольца (вставки) 2, х Штангенциркуль. Измерения не менее чем в трех точках равномерно по периметру 21.
Ширина расплавляемого кольца (вставки) 2, х То же 22. Длина сектора отвода (сварного) по наружной образующей 2, ц Линейка. Измерение детали в зоне максимального размера 23.
Длина сектора отвода (сварного) по внутренней образующей 2, ц Линейка. Измерение детали в зоне минимального размера 24. Угол наклона кромки сектора отвода (сварного) 2, ц Линейка и угломер или шаблон универсальный 25. Диаметр отверстия в корпусе (трубе) 2, ч, ш, э Штангенциркуль. Измерения в двух взаимно перпендикулярных сечениях (4 точки) 26.
Диаметр расточки в корпусе (трубе) 2, э То же 27. Шероховатость зачищенных поверхностей Профилограф-профилометр, образцы шероховатости (сравнения), измерительные датчики ДШВ. Контролируют поверхности, указанные в п.6.2.7 28. Расстояние до точки изменения углов разделки кромок 2, ю Штангенциркуль Примечание.
Допускаются другие способы и средства измерений, обеспечивающие требуемую ПТД точность измерения параметров подготовки деталей под сборку к сварке. Контролируемые параметры и средства измерений при сборке деталей под сварку Контролируемый параметр Условное обозначение параметра Номер рисунка Средства измерений. Требования к измерениям 1 2 3 4 1. Зазор в соединении 3, а, б, в, г, д, е, ж, и, к, с, т Щуп, шаблон универсальный. Измерение - см.
Специальный зазор 3, и, к Щуп. Измерение - см. Смещение кромок деталей с внутренней стороны соединения 3, а Линейка и щуп. Измерение - см. Смещение кромок деталей с наружной стороны соединения 3, а, б Линейка и щуп.
Измерение - см. Зазор между подкладной пластиной (кольцом) и внутренней поверхностью детали 3, б Шаблон универсальный или специальный. Измерения не менее чем в трех точках по длине (периметру) соединения 6. Смещение привариваемого элемента в угловом соединении 3, д Штангенциркуль, линейка.
Измерения не менее чем в трех точках по длине 7. Размер перекрытия деталей в нахлесточном соединении 3, б, е Линейка. Измерения не менее чем в двух точках по длине 8. Несимметричность штуцера 3, м Линейка. Измерения не менее чем в двух точках по длине 9. Смещение проволочной вставки с внутренней стороны 3, ж Штангенциркуль, шаблон или щуп. Измерения выполняются после прихватки вставки к кромке разделки одной из деталей 10.
Инструкция По Визуальному И Измерительному Контролю Рк
Зазор в замке расплавляемого кольца (вставки) - Шаблон универсальный или щуп. Измерения выполняются после прихватки вставки к одной из деталей 11. Несимметричность углового соединения труб.